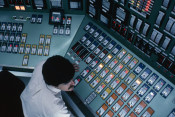
On-line monitoring
Strain sensors perform three separate functions in the monitoring of high temperature plant:-
Root Cause Analysis
While each component of a power generating plant is carefully designed to withstand specified temperature and pressure conditions, extraneous forces may act without the knowledge of the plant operators. Such forces arise from hanger failures, keyway friction, thermal expansion, boiler movements, etc. and often react at welds of rigid components such as steam chests, valve casings, turbines and headers. If such forces can be detected at an early stage of development, millions of Euros can be saved in unscheduled outage costs.
A useful aid to root cause analysis is the state of strain that will exist on the surface of a pressurised cylinder. Theoretically such strains will be zero since the ratio of circumferential to axial stress will be 2:1 and Poisson's ratio is 0.5 for steady-state creep conditions. Strain sensors positioned on the longitudinal axis of a pipe should therefore record zero strain. An output change from a longitudinal gauge could indicate the presence of 'system stresses' and further confirmation could be achieved if a sensor diametrically opposite recorded an output in opposite phase, i.e. component is bending.
The primary function of a root cause analysis is the detection of forces that are not designed to be present. Once the source of these extraneous forces has been established, corrective measures may be implemented to eliminate the unwanted stress.
Creep Strain Monitoring
The monitoring of creep strain in a power generation plant is an extremely demanding task. From the assumption in design that an allowable creep strain will be 2% in 20 years, we may derive an average creep strain rate of 0.1 x 10-6/hr. The measuring device must therefore have drift and stability characteristics of the order 0.1 x 10-7/hr.
Laboratory tests have demonstrated stability better than 0.1 x 10-7/hr is possible, however, ten key elements control the accuracy of gauges used in creep strain monitoring:
- Oxide growth underneath the sensor can cause 'rocking' with distortion of the output data.
- Poor thermal matching between sensor and test surface will generate an output under thermal transient conditions.
- Mineral-insulated cables are difficult to seal above 550oC.
- Long cable lengths induce noise and 'cross-talk'.
- In fossil-fuelled power plant sulphur may attack cables, seals and spot welds.
- Attachment of sensors to curved surfaces requires special calibration or sensor design modifications.
- When sensors are positioned above the test surface a geometric effect will occur if bending is imposed.
- Attachment of cables to sensor can introduce errors.
- Attachment of sensor to test surface can introduce errors.
- Stability and drift in electronics circuitry.
Note:- Above 700oC the effects of ionisation must also be considered.
To produce reliable creep strain data from power plant, all parameters identified must be addressed at design, manufacture and installation stages.
Defect Monitoring
Defect monitoring is the measurement of small displacements as a crack opens. Sensors are placed at the centre and each end of the crack to monitor growth and direction of cracking. The outputs recorded must be treated as displacements, not strain, however sensors will be influenced by the same key elements as those applying to creep monitoring.